top of page

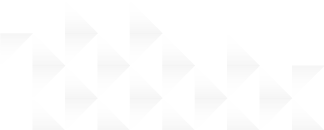
Frequently Asked Questions and Answers
Why is CJK using a process like cyanide leaching, which can be risky?
This project has tremendous benefits to the environment by helping reduce contamination to streams and rivers from historic mining operations. We acknowledge the hazards related to cyanide and have taken three important steps to ensure protection of the environment.
-
CJK uses industry-proven methods, such as cyanide detoxification, in order to meet the stringent regulations of both state and federal agencies with regard to its handling and use.
-
The majority of the cyanide used in the process is reclaimed and reused. Cyanide that cannot be reclaimed is destroyed using an industry-proven method prior to disposal in the lined tailings storage facility.
-
The Leadville Mill was designed and permitted as a zero-discharge facility, which means all water is recovered and contained, as well as waste materials.
For more details on these steps, see our Cyanide Handling Process
If there was a cyanide spill or one of the storage ponds overflowed, how would you clean it up before it reached the Arkansas River?
The mill facility will use well-understood, proven processes, standard in the U.S. gold mining industry, to ensure the environmental safety of its operations.
-
Typically, when a leak is detected, the plant will shut down, other tanks will be cut off, and the leaking tank will be drained and repaired. Sump pumps are designed to contain spills that may be encountered during this type of circumstance.
-
The mill is designed to encapsulate all solids and water used in the process.
-
Chemicals will be stored in overpack containers designed with a capacity 50% greater than their contents, per state and federal guidelines.
-
The process facility has an emergency containment sump to capture spills, should they occur. The capacity of the sump is over 2-times the capacity of all process liquids at any given time. A sump, meaning it is below the land surface makes it virtually impossible for discharges from the facility.
How is your company qualified to use cyanide?
CJK acknowledges the hazards related to cyanide, as well as other chemicals. There will be many checks and balances to ensure safe use. The handling and use of these chemicals are common in mining operations, and its safe use is highly regulated by the State (Colorado Department of Reclamation Mining and Safety-CDRMS, Colorado Department of Health and the Environment-CDPHE) as well as federal regulators (Mining Health and Safety Administration-MSHA). Cyanide will be detoxified, and metals of concern treated using the lime used in the milling process. CJK is required by law to comply with regulations associated with the handling and use of hazardous materials and will use these industry-proven methods.
The cyanide management plan is highly regulated by CDRMS and must be approved before operations can commence. Updated cyanide and emergency management plans will be included in the revised permit application which will be completed by the end of February, 2024.
Most of the cyanide used in the process is reclaimed and re-used. However, the cyanide that cannot be reclaimed will be destroyed using ferric sulfite prior to disposal in the Filtered Tailings Deposit (FTD). The cyanide detoxification process is an industry-proven method. Cyanide concentration in the FTD will be at a safe level.
How will you prevent airborne contamination during the excavation and transport of mine waste?
CJK has purchased and will have a dust monitor installed to monitor dust to assure it is below regulatory limits.
Mine waste material is generally damp. Nevertheless, the material surface will often be dry and dust control measures as required will be implemented. Roads will also become dusty. Roads will be sprayed with dust surfactants and water. Trucks will be covered during transportation. Material will be sprayed with water prior to loading in the crusher bin. The crusher facility will be an enclosed building with negative air pressure created by a dust collector. The material will be wet from the time it is introduced in the ball mill until it is deposited on the FTD. Water sprays as well as contemporaneous reclamation of the FTD will control dust from the tailings.
How will you deal with noise and ground vibration from your crushing operation and its potential impact on the nearby sewer line?
Using a methodology developed by the Federal Transit Authority, we have calculated impacts from our operation. The results indicate:
-
CJK has purchased and will have a vibration monitor installed to monitor and assure ground vibrations are below regulatory limits.
-
Vibration intensity at either the sewer line or anywhere at the wastewater treatment facility will be imperceptible.
-
Values are well below residential or commercial damage thresholds.
-
Vibrations experienced at the sewer will likely be lower in intensity than estimated.
What do you intend to do to prevent road damage and congestion/air pollution due to truck traffic?
These are important considerations that are currently in the development stage. CJK is in discussion with Lake County Community Planning and Development (CPD) to address these issues. We will also engage community stakeholders in finalizing this plan. Our current proposed plan of operation is designed to minimize truck traffic resulting from hauling of material to the mill. It is anticipated that there will be four tandem standard dump trucks in the fleet. It is currently contemplated that trucks will deliver 22 loads of material each day. The proposed route will not go through downtown Leadville and will circumvent neighborhoods. Traffic and pedestrian safety will be based on: avoidance of neighborhoods, high pedestrian traffic areas, daylight only operation, and slow speeds when close to populated areas. CJK will share the hauling route with the community once it is approved.
-
Truck hauling will be limited to 8-hour shifts during daylight hours.
-
Existing roads will be used, so there will be no additional impact in the forest.
-
While the mine permit allows for 80 truckloads per day, operations are expected to be closer to 40 per day (including work on slag piles).
Plans are in place to mitigate dust associated with operations.
-
Roads will be watered and dust suppression materials applied to eliminate dust.
-
Dust, resulting from crushing of material for the mill, will be in an enclosed building with a dust collection system. Dust generated by a loader into a feed hopper will be controlled by water spray.
Will the operations generate noise?
The mill will operate in accordance with Lake County’s noise ordinance. Trucks will be equipped with best practice mufflers. Back up alarms (as required by MSHA) will be of a broad band (white noise) sound type. Click here to hear the backup alarm. The crusher is small and will be located inside a sound-proof building. CJK has purchased monitoring equipment and will monitor noise to assure the above parameters are met and maintained.
The Mill claims there’s an ongoing mine waste problem in the Historic California District. What evidence is there that any such problem exist?
The California District contains many tons of acid-generating mine dumps. The area was designated an Environmental Protection Agency Superfund site in 1983. This historic mine waste contains metals including iron, which oxidizes, or rusts, that can form sulfuric acid. This acid leaches into the ground and streams flowing into the Arkansas River.
Our business plan is based on removing historic mine waste piles, recovering gold and silver from the waste, and restoring the sites back to natural conditions. Recovered gold and silver will make remediation economically viable. We also plan to remove historic smelter slag piles southwest of Leadville that can be used as road base aggregate. If successful, the Leadville community will be recognized as the pioneer of historic mine district remediation in the western U.S.
How is this work being coordinated with EPA’s California Gulch Superfund efforts?
All activities related to removing the historic low grade vein dumps on Breece Hill/Evans Gulch as well as the slag piles must conform with EPA’s Record of Decision. This document specifies what we can do and how we can do it. Additionally, the Colorado Department of Reclamation Mining and Safety (CDRMS) and Colorado Department of Public Health and Environment (CDPHE) work closely with EPA on all aspects related to the California Gulch Superfund site.
How does this benefit the environment?
Physically removing acid-leaching historic mine waste from the environment is a unique approach to the centuries-old problem of cleaning up mine waste. CJK’s innovative remediation plan will improve water quality in the upper Arkansas River and the health of the river and surrounding habitat. It will remove mine tailings and slag from the environment, creating natural spaces for wildlife, and serve as a template for the responsible clean-up of other historic mining districts. Both the Environmental Protection Agency and Colorado Department of Health and Environment support the work.
What happens to the waste pits after you’ve extracted all the gold and silver you can? Will they be monitored decades after you stop operating, to ensure there are no leaks, or will they just be abandoned like the mine waste you are processing?
Once the waste piles are removed, the areas will be restored to pre-mining conditions by planting native grasses and trees as required by the reclamation permit.
How much mine waste will be removed and processed?
Initially, CJK-owned material, totaling more than 1 million tons of low-grade vein dump material in the Breece Hill and Evans Gulch areas of the Historic California Gulch Mining District east of Leadville, will be removed and processed. Additionally, we plan to remove an estimated 1.3 million tons of slag.
Are you only addressing materials/mine claims owned by CJK?
Our plan is to initially process CJK-owned material but could expand to the cleanup of mine waste material owned by other parties.
Is the mill a good use of the local water supply?
The process plant doesn’t use water from the aquifer supplying nearby homes. Every effort will be made to recycle water, however any water needed will be supplied by Parkville Water District. No water will be pumped from wells, so the process will not threaten depletion of domestic well water users. The current plan calls for 20 gallons per minute (gpm).
Parkville Water District welcomes the addition of an industrial water client. Also, there is water available in the Arkansas River watershed for industrial mining and processing uses. Water laws do not permit this water to be used for other purposes. Similarly, water dedicated to agriculture cannot be used for anything except agriculture. Therefore, the use of water at the process plant will not affect agricultural, ranching, or other users. CJK prefers to access water from Parkville, as it is our understanding that Parkville welcomes us as a user, this water is available, and that an industrial client will result in an economic benefit to Parkville and the community.
How do you prevent the project’s Filtered Tailings Deposit (FTD) from infiltrating groundwater and impacting the plant’s sewer line?
It should be noted that the tailings will be filtered to about 25% moisture, which is like beach sand. The vast majority of the water will be entrained in the sand and will not flow out. Also, the FTD will be constructed in a very shallow 4H:1H slope, which is very stable for this material.
By code, the FTD (which includes the catchment pond) will be double-lined with leak detection to protect groundwater. Additionally, new up- and down-gradient wells will specifically monitor groundwater quality around the FTD. Groundwater infiltration from the FTD, in the unlikely event it occurs, will be detected by this monitoring system and will be the responsibility of CJK, not Leadville Sanitation which is upgradient from the process facility. In addition, the FTD design includes a 250-foot offset, assuring that it is not up-gradient from the wastewater treatment facility itself.
All surface water flows (e.g. rain and snow) from the FTD will be captured in a lined catchment pond. In the unlikely event of a catastrophic failure, all surface flows will be captured in the Emergency Containment Sump (ECS), which follows the natural drainage.
How long will it take to complete the cleanup?
CJK owns enough gold-bearing material to operate the mill for about 7 to 8 years. We estimate that the slag piles will also be processed in the same timeframe.
Could operations impact Leadville’s drinking water supply? How will you monitor that?
Both the mill and the slag operations are located on the southwest side of Leadville, which is down-gradient and quite distant from both domestic water wells, and Leadville’s water source, which is east and north of Leadville. The mill is a zero-discharge facility and will therefore not impact domestic water wells south and west of the mill. In the unlikely event of a spill, backup measures to protect surface and groundwater are in place, including the Emergency Containment Sump (ECS) which has the capacity to capture multiple times the fluid capacity of the mill in the event of a surface spill, and down-stream wells to pump groundwater plumes. Ground and surface water quality will be extensively monitored.
What happens to the slag after it’s removed? Will it be trucked out or processed at the mill?
The slag will be trucked out to customers to be used for road base aggregate. It will not be processed at the mill. The slag operation will be conducted during weekday daylight hours, and not expected to exceed 10 trucks per day during the annual construction season, and taper off during winter months. Ultimately, market demand will determine truck volume.
What are the days/hours of operations?
This is yet to be determined during our Conditional Use Permit Application (CUP) process. It is proposed the mill operate 24/7. However, all material deliveries and ore crushing will be during daylight hours.
How does this benefit the local economy?
The remediation activities, mill operation and slag removal will require 20–25 high paying positions. The need for supplies and services will also result in local economic benefit to the community.
bottom of page